Introduction of Continuous Stirred Tank Reactor
The Continuous Stirred Tank Reactor (CSTR) is a type of equipment widely used in the chemical industry for carrying out continuous chemical reactions. It operates by continuously introducing reactants into a well-mixed tank, where they undergo a reaction while being constantly stirred. The key feature of the CSTR is the continuous mixing of the reactants, which ensures uniformity of the reaction throughout the tank. This steady-state system allows for a continuous flow of reactants and a continuous withdrawal of the product stream.
The CSTR is known for its versatility, efficiency, and ability to handle a wide range of chemical reactions. It is widely used in processes such as polymerization, fermentation, and various other liquid-phase reactions. The CSTR’s design and configuration can vary depending on the specific requirements of the reaction, and it can be equipped with different types of agitators and temperature control systems.
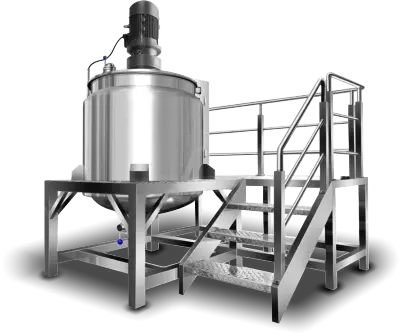
specification
Power
0.75-110 KW
Volume
0.03- 50000 L
Speed
Customized
Agitator Type
Top, Side, Bottom
Material
SS304, SS316, Carbon Steel
Temperature Control
Cooling, Heating, Insulation
Principle of Continuous Stirred Tank Reactor
The continuous stirred tank reactor (CSTR) operates based on the principle of a steady-state system, where the reactants are continuously fed into the reactor, and the product stream is continuously withdrawn. The key feature of the CSTR is the continuous mixing of the reactants, which ensures uniformity of the reaction throughout the tank. This is achieved by the use of an agitator, which helps in maintaining a high degree of mixing and preventing any concentration gradients within the reactor.
Advantages of Continuous Stirred Tank Reactor
The Continuous Stirred Tank Reactor (CSTR) offers several advantages that make it a popular choice in the chemical industry. Some of the key advantages of CSTRs are:
Continuous Operation
One of the major advantages of CSTRs is their ability to operate continuously. Reactants are continuously fed into the reactor, and the product stream is continuously withdrawn. This allows for a steady-state system, which is beneficial for processes that require a constant supply of reactants or products.
Uniform Mixing
CSTRs provide excellent mixing of reactants due to the continuous stirring action. The agitator inside the reactor ensures that the reactants are uniformly distributed throughout the tank, minimizing concentration gradients. This leads to better reaction efficiency and improved product quality.
Easy Scalability
CSTRs are relatively easy to scale up or down, making them suitable for both laboratory-scale experiments and large-scale industrial production. The continuous operation and well-mixed nature of CSTRs allow for consistent performance across different reactor sizes.
Versatility
CSTRs can accommodate a wide range of chemical reactions, including liquid-phase reactions, gas-liquid reactions, and multiphase reactions. They can handle both homogeneous and heterogeneous systems, making them versatile for various types of chemical processes.
Temperature Control
CSTRs are equipped with a temperature control jacket that allows for precise control of reaction temperatures. The jacket provides zones for heating, cooling, and insulation, enabling efficient temperature regulation throughout the reaction. This is particularly important for reactions that are sensitive to temperature changes.
Continuous Monitoring and Control
CSTRs offer the advantage of continuous monitoring and control of reaction parameters. Various sensors can be incorporated into the reactor to measure temperature, pressure, pH, and other relevant parameters. This allows for real-time adjustments and optimization of reaction conditions, ensuring consistent and desired outcomes.
Safety
CSTRs are generally considered safer compared to batch reactors since they operate under continuous conditions. The continuous flow of reactants minimizes the risk of sudden pressure buildup or uncontrolled reactions. Additionally, the uniform mixing reduces the likelihood of localized high concentrations that could lead to thermal runaway or other safety concerns.
Energy Efficiency
The continuous operation of CSTRs can result in improved energy efficiency compared to batch reactors. The ability to maintain a steady-state system allows for better heat integration and optimization of energy usage, leading to potential energy savings.
SeFluid's advantages for producing Continuous Stirred Tank Reactor
SeFluid is a leading manufacturer of Continuous Stirred Tank Reactors, known for its expertise in engineering and design. Here are some of the key advantages offered by us:
Customizable Designs
SeFluid offers customized designs tailored to clients’ specific requirements. Their reactors can be designed with different sizes, materials, and configurations to suit diverse applications and industries.
High-Quality Materials
SeFluid uses only premium-quality materials in the construction of their CSTRs, such as stainless steel, hastelloy, titanium, and other corrosion-resistant alloys. These materials ensure durability, reliability, and resistance to harsh operating environments.
Advanced Mixing Technologies
SeFluid incorporates advanced mixing technologies into their CSTRs, including impellers, turbines, and static mixers. These technologies guarantee efficient mixing and heat transfer, enhancing overall reactor performance.
Precision Engineering
SeFluid employs state-of-the-art manufacturing techniques and precision engineering to produce reactors with exceptional dimensional accuracy and surface finish. This attention to detail ensures reliable operation and minimal maintenance requirements.
Stringent Quality Control
SeFluid adheres to strict quality control standards and procedures to ensure that every CSTR meets the highest levels of performance and safety. Their reactors undergo rigorous testing and inspection before delivery, providing customers with peace of mind.
Comprehensive Support
SeFluid offers comprehensive support services, including installation, commissioning, training, and maintenance. Their experienced team is always available to assist customers with any queries or issues, ensuring smooth and efficient operation of their CSTRs.
Request for Quotation
NEWS
CONTACT
No 28, Fengxia Rd, Hefei, Anhui Province, China 201400
Phone: +86 156 6910 1862
Fax: +86 551 5843 6163
sales@sefluid.com