Introduction of Industrial Mixing Tank with Agitator
The industrial mixing tank with agitator is a versatile and essential equipment widely used in various industries. It plays a crucial role in processing for various industries and are widely applied. The whole tank system is designed to facilitate effective blending and mixing of ingredients, ensuring homogeneous mixture and uniform consistency of end products.
With years of expertise in manufacturing industrial mixing tank with agitator, SeFluid’s products embody excellence. We utilize the finest materials, ensuring durability and precision engineering. Our tanks undergo meticulous polishing and finishing, showcasing a fine exterior. Backed by an experienced engineering team, we are professional in designing fluid processing equipment solutions. Trust SeFluid for unrivaled quality, innovation, and customer satisfaction. Experience the SeFluid advantage today!
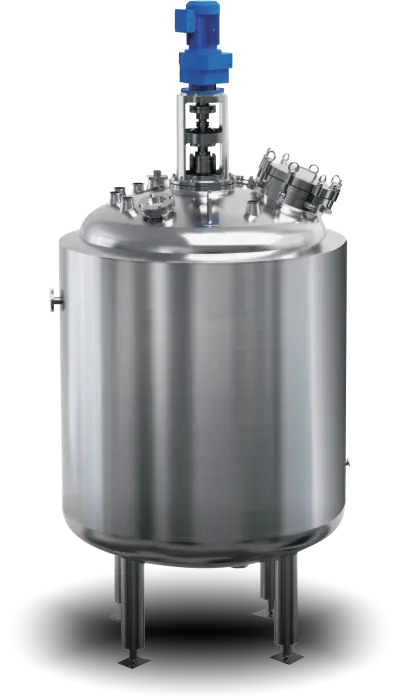
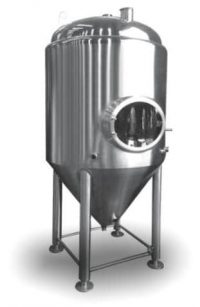
specification
Power
0.75-110 KW
Volume
0.03- 50000 L
Speed
Customized
Agitator Type
Top, Side, Bottom
Material
SS304, SS316, Carbon Steel
Temperature Control
Cooling, Heating, Insulation
Principle of Industrial Mixing Tank with Agitator
The working principle of industrial mixing tank with agitator involves creating turbulence within the contents of the vessel to achieve uniformity in blending and prevent settling or separation of solids and liquids. The primary mechanism for achieving this goal is via agitation, achieved through rotating blades or impellers mounted on a central shaft powered by an electric motor or hydraulic drive unit.
As the blades spin, they draw fluid towards the center and then expel it radially outward, creating a vortex-like motion known as “circulation.” This circulation leads to constant mixing of all components within the tank. Depending on the application, the agitation speed, direction, and intensity can be controlled to achieve optimal results.
Baffles or deflectors may also be installed in the tank to redirect the flow of liquid, increasing contact between particles and promoting homogenization. They can be fixed or adjustable, allowing operators to optimize mixing conditions depending on changing process demands or product characteristics.
The choice of blade design depends on the desired level of shear, viscosity of the material being mixed, and required blend uniformity. Paddle mixers offer gentle agitation while maintaining good heat transfer properties, while impellers generate higher shear rates for more aggressive mixing.
In summary, the working principle of industrial mixing tanks with agitators revolves around agitation created by rotating blades or impellers, enhanced by baffles or deflectors, to achieve consistent blending and mixing of substances within the tank.
Benefits of SeFluid's Industrial Mixing Tank with Agitator
Looking for the perfect solution to meet your industrial mixing needs? Look no further than SeFluid, the leading manufacturer of Industrial Mixing Tanks with Agitators. With our unparalleled expertise and cutting-edge technology, we bring a range of advantages to the table:
Precision Engineering
Our Industrial Mixing Tanks with Agitators are meticulously designed and engineered to deliver exceptional performance. Each tank is crafted with precision, ensuring efficient mixing, blending, and homogenization of various materials.
Superior Quality Materials
We understand the importance of durability and reliability in industrial processes. That’s why we use only the highest quality materials, such as stainless steel, carbon steel, and fiberglass-reinforced plastics (FRP), ensuring longevity and resistance to corrosive substances.
Versatile Agitation Solutions
At SeFluid, we offer a wide range of agitator options tailored to your specific requirements. Whether it’s top-entry, side-entry, or bottom-entry agitators, we have the expertise to customize the most suitable solution for your industrial processes.
Unmatched Performance
Our Industrial Mixing Tanks with Agitators are engineered to deliver outstanding performance, meeting even the most demanding industrial applications. From blending chemicals in the chemical industry to homogenizing pharmaceutical formulations, our tanks ensure optimal results.
Industry Expertise
With years of experience and a team of dedicated experts, SeFluid understands the unique challenges and requirements of different industries. We work closely with our clients to provide customized solutions that maximize efficiency and productivity.
Types of Agitators for Industrial Mixing Tank
Top-Entry Agitators
For this type, the agitators are mounted on the top of the tank and are commonly used for blending and suspending materials. They are versatile and can handle high-viscosity and low-viscosity fluids.
Side-Entry Agitators
These agitators are installed on the side wall of the tank and are primarily used for continuous mixing and circulation. They are commonly found in large-scale industrial processes.
Bottom-Entry Agitators
These agitators are mounted at the bottom of the tank and are designed for applications that require intense mixing and heat transfer. They are suitable for processes such as crystallization, fermentation, and dissolution.
Advantages of Industrial Mixing Tank with Agitator
Improved Mixing Efficiency
Industrial mixing tanks with agitators provide consistent and thorough mixing, reducing processing time and improving productivity.
Uniform Consistency
The agitators ensure a uniform distribution of ingredients throughout the liquid, leading to better quality end products. 3. Customizable Designs: The tanks can be customized to suit specific needs, whether it’s the size, shape, material, or configuration.
Customizable Designs
The tanks can be customized to suit specific needs, whether it’s the size, shape, material, or configuration.
Low Maintenance
The design of these tanks is relatively simple and durable, requiring minimal maintenance and repair.
Energy Efficient
By using the right kind of agitator, energy consumption can be optimized for maximum efficiency.
Temperature Control for Industrial Mixing Tank with Agitator
Temperature control is a critical aspect of industrial processes involving mixing tanks with agitators. The ability to heat, insulate, and cool the contents of the tank ensures optimal conditions for various applications. Here are the common temperature control methods employed:
Heating
Heating in an industrial mixing tank can be achieved through different methods, including:
Steam Jackets
Tanks equipped with steam jackets allow for indirect heating. Steam circulates within the jacket, transferring heat to the tank contents through conduction.
Electric Heating Elements
Electric heating elements immersed in the tank heat the liquid directly. They provide precise temperature control and are suitable for applications requiring quick heat-up times.
External Heat Exchangers
Heat exchangers connected to the tank enable heat transfer from an external source, such as hot water or thermal oil.
Insulation
Insulation is crucial for maintaining the desired temperature and minimizing heat loss. Common insulation methods for industrial mixing tanks include:
Insulated Jackets
Tanks can be fitted with insulating jackets, typically made of materials like foam or fiberglass, to reduce heat transfer to the surroundings.
Insulating Foam or Panels
Additional insulation can be applied directly to the tank walls using foam or insulating panels, providing an extra layer of thermal protection.
Cooling
Cooling is necessary in processes where temperature control is essential for product quality or safety. Cooling methods for industrial mixing tanks include:
Cooling Coils
Tanks can be equipped with cooling coils through which a chilled medium, such as refrigerant or chilled water, circulates. The coils absorb heat from the tank contents, lowering their temperature.
External Chiller Units
Chiller units connected to the tank facilitate the transfer of heat from the liquid to a refrigerant, cooling the contents to the desired temperature.
Effective temperature control in industrial mixing tanks with agitators ensures optimal process conditions, enhances product quality, and improves overall efficiency. The choice of heating, insulation, and cooling methods depends on the specific process requirements, the characteristics of the materials, and the desired temperature control range.
Applications of Industrial Mixing Tank with Agitator
Industrial mixing tanks with agitators find applications in a wide range of industries, including:
Chemical Industry
These tanks are used for mixing chemicals, blending different components, and facilitating chemical reactions.
Pharmaceutical Industry
They are utilized for the preparation of liquid formulations, dissolution of solids, and homogenization of pharmaceutical products.
Food and Beverage Industry
These tanks play a crucial role in the production of beverages, sauces, dressings, and other food products, ensuring uniformity and consistency.
Water and Wastewater Treatment
Industrial mixing tanks with agitators are employed in processes such as coagulation, flocculation, and neutralization, aiding in the purification of water and treatment of wastewater.
Petrochemical Industry
These tanks are used for mixing and blending various petrochemical products, such as fuels, lubricants, and additives.
Request for Quotation
NEWS
contact
No 28, Fengxia Rd, Hefei, Anhui Province, China 201400
Phone: +86 156 6910 1862
Fax: +86 551 5843 6163
sales@sefluid.com