Introduction of Bead Mill
The bead mill, also referred to as the sand mill, is a kind of milling equipment used for particle size reduction and dispersion of solid particles in a liquid medium. The working of a bead mill is based on intense agitation and grinding between the solid particles and the grinding media (beads) within a cylindrical chamber. The chamber is typically filled with grinding beads made of materials such as zirconia, ceramic, or metal. There is an agitator in the chamber, usually in the form of a rotating shaft with discs or pins attached. Its high-speed rotation generates a strong turbulent flow within the chamber, causing the grinding beads and the material to collide and interact.
As the material is fed into the mill from one end, it is subjected to the high shear forces generated by the agitator and grinding beads. This intense agitation breaks down the particles, reducing their size and promoting dispersion. The grinding beads effectively grind and disperse the material, ensuring a uniform particle size distribution in the final product.
Compared with similar products from other competitors, SeFluid’s bead mill series are cost-effective and easy to maintain with an economic price that customers can afford but can achieve nano-level grinding fineness. In many fields such as coatings, rubber, pesticides, cosmetics, etc., SeFluid’s bead mills are widely used and widely welcomed by users.
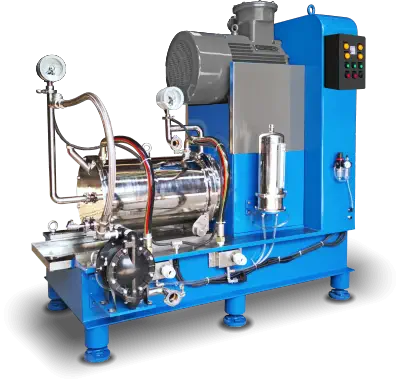
specification
Power
11-55 kw
Cylinder volume
10-100 L
Speed
700-1200 rpm
Fineness
nano level
Principle of Bead Mill
There are a group of cylindrical agitating rod pins installed on the hollow rotor shaft. These pins work with the horizontal ceramic shell to form a high-density energy grinding chamber. There are different materials for the pins according to different material properties. When running, the hollow stirring shaft drives the rod pins to do high-speed operation. Then, the rod pin drives the medium to carry out fierce collision and grinding. Therefore, the medium experiences strong impact force and high shear force. After that, good milling and dispersing effect will be achieved.
Key Parts of SESM Bead Mill Series
Cooling System
Jacketed water circulation chamber wall cooling; Discharging end cover cooling; Mechanical seal pressurized tank cooling & heat exchange cooling.
Control System
Standard electronic control system: host electric control cabinet with on-site control box, easy for spot operation. Top brand electric components.
Mechanical Seal
Dedicated double end mechanical seal, easy to remove and install. No need of professional people for replacement. Independent cooling system.
Bead Mill Gauge
Electric pressure meter and electric temperature meter (with temperature protection & pressure protection, auto-stop function).
Milling Bead
Pure zirconia beads (more than 95% zirconium content) for bead mill.
Feeding Pump
Pneumatic diaphragm pump, all aluminum alloy housing, Teflon membranes.
Milling Cylinder Material
Inside: Hard alloy or ceramic
Outer materials: SS304/SS316 or else, mirror polished.
Product Discharging
ACC centrifugal turbine, static large area radial direction sieve; High output, no beads damaged or blocked.
Advantage of SESM Bead Mill Series
Silicon Carbide Inner Milling Cylinder
In SeFluid’s series of bead mill, we take silicon carbide ceramic as grinding cylinder material. It is sintered over many days at high temperatures. As the hardness of silicon carbide is second only to diamond, it is highly wear resistant and long lasting. Meanwhile, it has high strength, high hardness, excellent wear and corrosion resistance and good temperature resistance (-50℃ to 1350℃). In addition, the smooth surface of silicon carbide ceramic can prevent dust accumulation. So, it is ideal material for milling parts.
Long Life Milling Assembly
Rotor assembly is one of the key parts of an agitator bead mill. It is also the final kinetic energy conversion device. Due to the high speed of rotation, the rotor assembly must be highly resistant to fatigue, corrosion and abrasion. Therefore, it is made of special materials and subjected to many rigorous tests, depending on the customer’s material requirements. This ensures that our bead mill series achieves consistent and efficient grinding performance. For all SeFluid’s bead mill products, we have various wear resistant materials for user’s options ranging from ceramic to hard alloy.
Cartridge Mechanical Seal Adopted
Modular design is adopted in the use of cartridge mechanical seals, where the seal module is directly installed on the bead mill shaft during installation. During maintenance, only the seal module needs to be disassembled, without the need to dismantle other components such as bearings. This greatly simplifies the installation process and reduces maintenance costs.
When a bead mill is in operation, a large amount of grinding fluid is generated. If the seal is not tight, it can lead to leakage of the grinding fluid, which can affect the normal operation of the equipment and even cause safety accidents. Moreover, the grinding fluid can enter the bearings, resulting in damage to the bearings. Cartridge mechanical seals have excellent sealing performance, effectively preventing leakage of the grinding fluid, protecting the normal operation of the bearings, prolonging the service life of the equipment, and reducing operational costs.
High Efficiency Cooling Systems
Good cooling is necessary to ensure the long-term stable running of a bead mill. If the large amounts of heat are not removed in time, the mechanical seal and milling parts are apt to be damaged. Meanwhile, the milled material can also change its physical or chemical properties due to the high temperature. In SeFluid’s bead mill series, we have specially designed two efficient cooling systems. Firstly there is an oil circulation cooling system for the mechanical seals. Secondly, there is a jacket cooling system for the grinding cylinder. Moreover, the system allows users to keep track of the temperature rise.
Request for Quotation
NEWS
contact
No 28, Fengxia Rd, Hefei, Anhui Province, China 201400
Phone: +86 156 6910 1862
Fax: +86 551 5843 6163
sales@sefluid.com